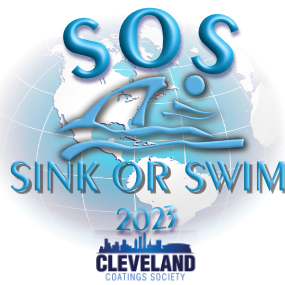
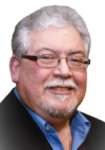
Ben Carlozzo,
SOS Chair
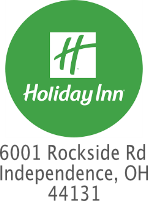
Request the CCS/SOS
Rate Special
216-524-8050
Keynote Speaker:
âTHE CASE FOR SUSTAINABILITY AT PPGâ
Diane Kappas, Vice President, Global Sustainability
Diane Kappas is the PPG vice president, global sustainability and is accountable for leading the company's efforts to incorporate a positive environmental, social and governance (ESG) impact into core business strategies and functions, enabling the company to reduce its environmental impact, creating positive social impact and growing sales by creating sustainable solutions for customers. Â Â Diane assumed this role in July 2021.
Prior to this newly created position at PPG, Diane was the vice president, automotive coatings, Americas and vice president, protective and marine coatings, Americas where she had P&L responsibility for the businesses in the region.
Diane has worked at PPG for 38 years across multiple product platforms including optical monomers, automotive replacement glass, specialty chemicals, architectural coatings, industrial coatings, protective and marine coatings, refinish coatings and automotive coatings. She has held a variety of roles in manufacturing, supply chain, quality management, procurement, human resources, EHS and general management prior to moving into her current role.
A native of Pittsburgh, Diane earned a Bachelor of Science in chemical engineering from the University of Pittsburgh and a Master of Business Administration from Duquesne University.
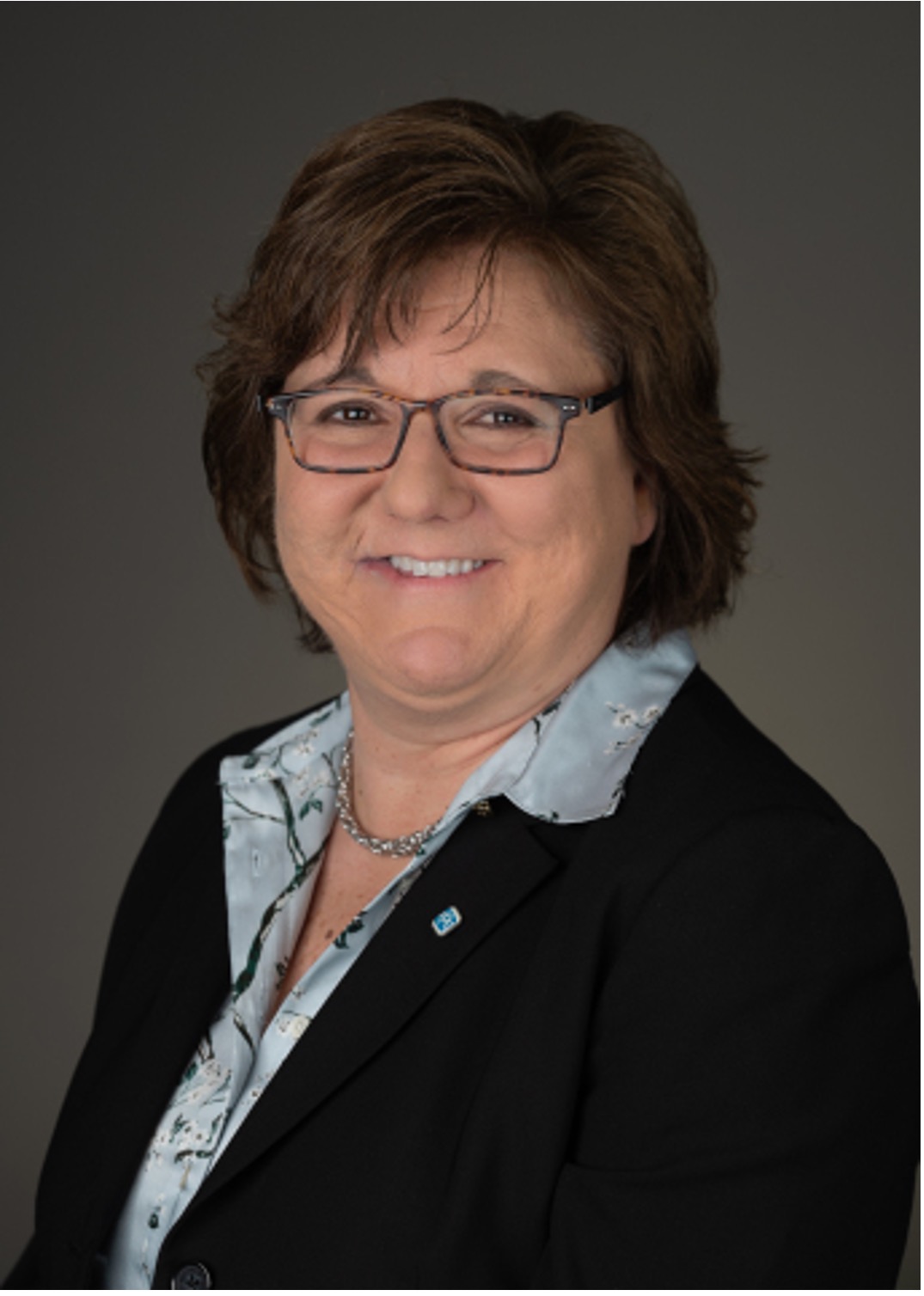
Diane Kappas
Vice President,
Global Sustainability
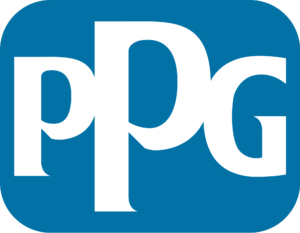
SOS Program Abstracts
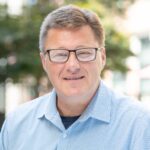
Bruce Berglund, CHT USA
There are increasing demands for higher performance, more sustainable coatings employing more natural materials with substantial health, safety, and environmental properties. To address those challenges raw material suppliers and coatings manufacturers are increasingly turning to water-based solutions that require efficient, environmentally friendly emulsion technologies. The science behind key wax and silicone emulsion technologies to meet these needs will be presented. Having a fundamental understanding of emulsion principles provides for more effective development when designing high performance coating raw materials. A new wax emulsion technology will be presented that utilizes paraffin-free, natural waxes with surfactant packages that produce extremely high regulatory compliance formulations. These novel barrier additives provide water and oil repellency, block resistance and water beading while reducing or even preventing water vapor permeability. New silicone, low cyclic content, gum emulsions will also be presented. They also have high regulatory clearances. These low VOC, low cyclic content, silicone additives provide slip, haptic properties and resistance to water, scratching, abrasion, and blocking.
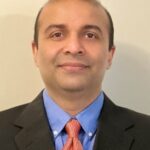
New Thermal Management Raw Materials Platform Gives Flexibility to Develop Next Generation Thermal Insulation Coatings (TIC) with Improved Performance
Hrishikesh (Rishi) Bhide, Evonik Corp.
Coating industry trends has driven increased use and interest to develop more efficiency and durable thermal insulative coatings. The key areas for this expansion are to reduce corrosion under insulation, increase occupational safety and reduce energy loss. Key features of these water-based coatings are low thermal conductivity, high hydrophobicity and adhesion along with an emerging interest to have greater heat resistance and stability. This paper will introduce a new water-based, silicone hybrid binder and two novel microporous composite granules; one with high thermal insulative efficiency and the other, a pure hydrophobic synthetic silica pearl shaped filler to optimize thermal insulation efficiency as well as offering mechanical stability and reduced cracking in these highly filled coatings. The new platform offers the formulator options to leverage all new technologies together or separately when a compatible binder is needed to increase thermal heat stability, and or new fillers are needed to achieve low thermal conductivity and improve mechanical stability by reducing cracking in highly filled coatings. Coatings and formulating details will be highlighted.
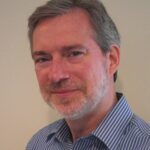
Eight Things You Probably Donât Know About the Electric Heaters in Your Fluid Dispensing System
Michael Bonner, Saint Clair Systems, Inc.
It seems that everything from automobiles to water heaters is going electric these days, so you probably think youâre on the leading edge because your coating temperature control system is comprised of electric drum blankets and in-line electric heaters. And you did it before it became popular! Unfortunately, there are little-known flaws in this approach that could be causing failures in your fluid dispensing system instead of addressing the problems you set out to solve. In this presentation we reveal eight ways that electric heating systems can create issues in both manual and automated coating application operations. Each of these is explained in detail and supported by the underlying science of modern coating and application technologies. This provides a roadmap by which to analyze issues and improve your performance, to realize the benefits you set out to achieve when you selected your electric heating system in the first place!
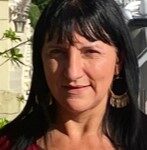
Novel Dispersant for Zero VOC Architectural Paints with Improved Open Time and Freeze/Thaw Stability Development
Celia Szcypula Buono, Nouryon Functional Chemicals, LLC
Open time is the length of time the paint film remains âwetâ or open enough to allow âworkabilityâ when paint is applied with a brush or roller. Open time is a key performance vector for paint and coatings, especially for better one coat hiding. In waterborne or latex coatings, the film formation phenomena controls that mainly controls open time. Currently formulators use a co-solvent or coalescent which slows down the evaporation of water during the film drying process to increase open time. However, these glycol solvents contribute to the volatile organic content (VOC) and this is a serious issue since the goal of most formulations is zero VOC. In addition, the type and amount of coalescent may lower the glass transition temperature (Tg) of the binder, leading to a softer film which improves resistance to cracking but negatively affects dirt pick up. Paint and coating formulations are usually produced in a 2-step system: an initial grind stage and a final let down stage. In the grind stage, the dispersant (usually a polymer) and pigment particles are subjected to very high shear rates to ensure that the pigment particles are in the desired (smaller) particle range that is necessary for optimum performance such as hiding. The pigment dispersant polymer is key to keep pigments from agglomerating, promoting stability of the final product and avoiding syneresis and pigment precipitation during storage. The structure generated in the formulation by the pigment dispersion is also key to improving water resistance and obtaining good color development. Glycol type solvents are typically used in the grind stage to minimize water lost due to the high temperatures generated by the high shear speeds. However, glycols can generate a lot of foam which then necessitates the use of a defoamer. This presentation will discuss the benefits with a novel pigment dispersant polymer for zero VOC architectural paints. This novel dispersant eliminates the need for a glycol (co-solvent or coalescent) as well as a defoamer in the formulation. The resulting formulation incorporating this novel dispersant improves film formation, open time, freeze/thaw stability and color development, as well as adhesion, while lowering the total formulation cost.
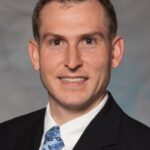
Waterborne Resins for the Evolving Environmental and Sustainability Coatings Market
Eric Broz, Lubrizol
The need for new resins and polymers that allow formulators to develop coatings in compliance with changing environmental and sustainability regulations is crucial for todayâs market. Whether chemists are formulating for things like wood, concrete, or metal applications, it is important that these new technologies perform similarly or in most cases, outperform current benchmarks. This presentation will highlight the various advancements in Lubrizolâs resins and polymers that are APEO and formaldehyde free, allow for lower VOC formulations or have high (50%) renewable content. Reviewing data generated in industry related formulations, we will focus on how these polymers maintain and enhance the chemical and stain resistance, adhesion, appearance, and other application properties while enabling formulations to pass the most stringent regulations and demand for âenvironmentally conscientiousâ products.
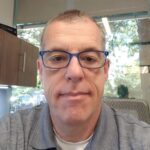
Mike Praw
The emulsion polymerization process to generate vinyl-acrylic latexes can be complex and the replacement of APE-based surfactants for EHS-friendly solutions can be challenging. The higher polarity of the polymer decreases surfactant adsorption and can also decrease the water resistance of the final coating; hence, surfactant choice is crucial in the development of resilient formulations. The effect of APE-free nonionic surfactants with different hydrophobes and APE-free anionic surfactants with different ethylene oxide content in the emulsion polymerization of vinyl-acrylic latex was investigated in terms of particle size, filterable solids and stability. The results were compared against vinyl-acrylic latexes synthesized with APE-based and APE-free surfactant benchmarks. A 45% PVC paint was formulated and the vinyl-acrylic latex synthesized with the optimized APE-free surfactant ratio increased wet scrub resistance in 200% when compared against the APE-free benchmark surfactants and 230% increase when compared against the APE-free latex commercially available.
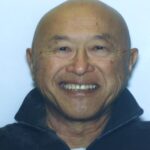
Controlling the air liquid interface
John Du, Patcham USA
Why and how to control the air/liquid interface for formulating the perfect coating: Air or more specifically, air/ coatings formulation interfacial interactions can cause manufacturing challenges as well as compromise coatings performance. This presentation will discuss the unfavorable air/liquid interactions that cause air entrapment and its stabilization in coatings. The consequence of under or over usage will also be covered in detail. Finally, how to properly select the type, dosage, and point of addition will be discussed with the goal of sufficient defoaming for manufacturing, storage, application and film formation without creating or causing coating defects.
__________________________________________________
SHORT COURSE:Â Introduction to Additives Technology
Introduction to Additives Technology
Syllabus for 2023 SOS Symposium
Additives â Why do we need them and what do they bring to our formulations
Why do we paint objects?
- Beautify, and Protect
What is paint?
- Binder for film formation
- Pigment for color
- Solvent to ease manufacturing and application
Discussion of the various different chemical interfaces and their interactions
- Pigment/air interface
- Pigment/solvated binder interface
- Air/solvated binder interface
- Substrate/coating interface
- Multiple other interfaces will be discussed
The role of additives in address the different interfacial chemistries
The Additives used by our industry for
- Pigment dispersion and stabilization
- Defoamer and Deaerating additives
- Surface leveling additives
- Rheology modifying additives
- Spacer additives for improving cost and film performance
To be given by John W Du.
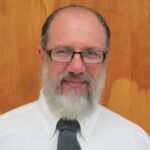
Renewable Biobased Multipurpose Coatings for Wood Finishes
David Folkman, Alberdingk Boley
As binders for coatings are continually pushed to be more environmentally friendly to meet increasing sustainability requirements, resin suppliers have responded with a variety of solutions. These efforts have resulted in a wide variety of new and innovative polymer design to meet environmental compliance while maintaining performance. Increasing developments in renewable biobased products have led to new and exciting possibilities in various market sectors including decorative, architectural, packaging and automotive coatings. The scope of this presentation will focus on the application of wood finishing using resins derived, whole or in part, from biobased sustainable sources. These resins will allow the formulator the ability to make âgreenerâ finishes than previously possible without compromising durability and high performance. A range of biobased products will be discussed including one and two component systems and interior wood stains and performance benchmarked against traditional products made from petroleum based raw materials.
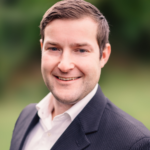
High Molecular Weight Silicone Emulsions: Preparation, Properties, and Applications
Robert Graff, CHT USA
Polydimethylsiloxanes or silicones are a highly unique class of polymers that are utilized in almost every industry. They can be varied over a broad range of molecular weights, organic modifications and branching structures and utilized in both water based and anhydrous formulations. Silicone emulsions are inert, heat stable, non-toxic products which suit many applications where lubrication, gloss, antistatic, protective and release properties are advantageous. High molecular weight linear polysiloxanes with viscosities that exceed 20 million centipoise (cP) also frequently referred to as silicone gums, find many applications in the coatings market. High molecular weight silicone emulsions are important in the coatings industry as they function as slip and anti-mar additives for both aqueous and non-aqueous coatings. They can also help to significantly increase the scratch resistance, increase gloss, and decrease whitening. Preparation of aqueous mechanical emulsions of silicone gum is difficult due to the handling of highly viscous materials and requires specialized processing equipment and emulsifiers. These emulsions are typically prepared using a specialized surfactants based on a siloxane copolymer resin. A drawback to these types of emulsions is that they contain xylene and other undesirable substances that are present during the manufacture of the siloxane copolymer resin.
Silicone gum can also be emulsified using specialized equipment such as a twin screw extruder. However, the costs for such equipment are relatively high, both from a capital and an operational standpoint. The preparation, properties and applications of such emulsions will be discussed as well as new advancements in the processing of these emulsions. Parameters including particle size, emulsifier system and silicone molecular weight were examined.
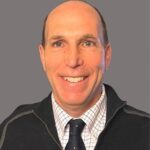
Highly Weather Resistant Aqueous Based Coatings using PVDF-Latex Hybrid Dispersions
Jeffrey Hamilton, Arkema
Polyvinylidene Fluoride (PVDF) coatings have been the industry standard for exterior architectural applications for over a half century. PVDFâs carbon-fluorine (C-F) bond, one of the strongest bonds known, provides performance attributes other alternative coating systems cannot match. Coatings containing PVDF can provide excellent weather resistance, UV stability, fade resistance, and gloss retention making them highly desirable coatings for architectural applications. To enhance their sustainability, beyond extended service life, an aqueous Polyvinylidene Fluoride (PVDF)-latex dispersion-based coating was developed. These coatings exhibit the same attributes including mold resistance, mildew resistance, and dirt pick up resistance in exterior coating applications. Coatings formulated with these dispersions continue the tradition of meeting AAMA 2605, 625, and 615 specifications. They also exhibit excellent south Florida weather resistance for over 20 years of exposure. Therefore, increasing the lifetime of the coating, while decreasing the need for recoats (VOC emissions), downtime and overall cost to the building owner. Combining the attributes of PVDF into a waterborne dispersion with a prolonged end-use service life, makes these coatings a more sustainable solution.
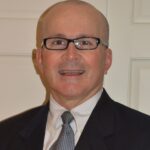
Coating Process - The Phases & Methodology to Implement a Successful UV Coating Project from Start to Finish
Michael Kelly, Allied PhotoChemical, Inc.
UV coating technology for General Manufacturing - So you can produce faster, small footprint and Clean - No emissions. Benefits: Sustainability / Environmental Advantages - No VOCâs or HAP's. Great Overall Process Improvements - Faster Production Speed. Improved Product Performance. Lower per linear foot coating costs. Sustainability / Environmental Advantages: - No VOC's - No Volatile Organic Compounds- No HAPâs - No Hazardous Air Pollutants- Non-Flammable- No solvents, waters or fillers- No humidity or temperature production issues. Great Overall Process Improvements: - Very fast production speeds - Upward of 800-900 feet per minute- Small physical footprint - Less than 35 feet- Minimal Work-in-Process- INSTANT dry - No post-cure- No downstream wet coating issues- No Zahn cup needed - Coating requires NO adjustment- Shift change / maintenance / weekend shutdowns - Just leave UV coating - No issues. Improved Product Performance: - Improved Humidity Testing results- Great Salt Fog Testing results- Ability to adjust coating attributes / color- Clear coats, metallics and colors available. Lower per linear foot coating costs: - ROI calculator comparing Water-based and UV coatings demonstrates coating savings- UV is typically lower cost.
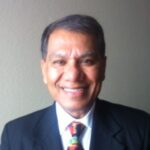
Color Sells - Colorants for Consumer Articles & Other Unique Applications
Romesh Kumar, Heubach Colorants, LLC
Surveys have shown that brightly colored goods sell for 10-20% higher price than those with neutral shades. In grocery and department stores, brilliant appearance articles are strategically placed to attract consumers. Bright and high chroma colors are generally associated with better quality and often selected over the duller shades. Consumers today desire a variety of options to color coordinate home interiors & bathrooms, and in household appliances, like hair dryers, glass ware etc. Small vehicles like Golf Carts, Scooters and E-Bikes painted in a variety of special and metallic finishes increase the market penetration. This presentation will describe unique set of highly transparent colorants which are excellent for formulating such finishes for appliances, vehicles, consumer goods, backlit signs, and many other applications. These colorants are bright (high chroma), have excellent performance, and are based on halogen free pigments (eliminating issues with incineration). The array of colorants allows formulators the flexibility to produce a variety of appearances on metal, wood, plastics, and other substrates in a relatively short time. These colorants are dispensable with automatic machines, and compared to dyes, have no risk of bleeding and migration into the topcoats. Complex shades (e.g. with effect pigments), and special effect appearances created by application over light and dark substrates and varying the film thickness. This all translates to better color choices in a âWhile You Waitâ set up that improves a productâs value and attracts customer; all with the help of brilliantly color coatings. Combination of unique pigments, milling technology and additives are key to these super transparent dispersions with high durability, and consistent quality. Dispersions for both water and solvent based systems will be discussed.
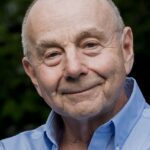
Demystifying Tg and MFFT in Waterborne Film Formation
Sam Morell, SamMorell.com
The are many factors that influence good film formation of waterborne coatings whether the polymer chemistry is based on all acrylic, styrene acrylic, vinyl acetate, etc. The glass transition temperature, or Tg, of the polymer and the minimum film formation temperature, or MFFT, of the coating formulation depend on many variables including monomer composition, polymer particle size, coalescing agents, hydroplasticization, application temperature, etc. This presentation will initially review the waterborne film formation process and subsequently dive deeper into an understanding of the differences between Tg and MFFT as well as the factors that influence each of those parameters.
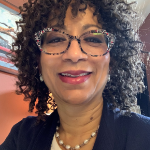
Future of Intumescent Coatings
Latoska Price, Synthomer
Intumescent coatings with its passive fireproofing capability is a subject area that has increased interest. Usually thought of as passive fire protection for structural steel used in high-rise structures, there is increased interest in intumescent coatings for substrates such as wood since more building frames are using wood in construction. While no material is entirely fireproof, the use of intumescent coatings can help slow the spread of fires and provide valuable escape time in the event of an emergency. This presentation will provide an overview of intumescent coatings with explanation on how they are formulated, current uses and future developments.
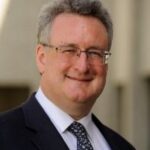
Replacing Fluorine-Based Additives in Coating Formulations
Jim Reader, Evonik Corporation
Many coatings formulators are now having to find alternatives to fluorosurfactants responding to potential or increased regulations. The lack of availability of mainstream technology is also another major reason for many to seek alternatives. Reformulation can be difficult, due to the unique multifunctional properties and chemical stability of the fluorosurfactants, so often replacement is not 1:1. Fluorosurfactants and additives are relatively low molecular weight additives containing fully (per) or partly (poly) fluorinated carbon chains connected to different functional groups. These additives are highly efficient at lowering the surface tension of liquid coatings to improve the wetting of substrates and eliminate film defects. They can also improve the stain and chemical resistance of coatings and improve slip and mar resistance. Formulators seeking alternatives to fluorosurfactants need to consider all the potential effects that these additives can bring to a formulation and then identify alternatives that can provide similar performance. This paper will compare different additive families and review how these additives or combinations of additives can be used to replace fluorosurfactants when needed.
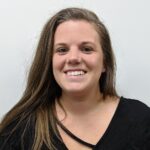
Improving Durability in Alkyd Coatings with Novel Catalyst Technology
Kellie Salerno, Borchers, A Milliken Brand
Oxidatively cured coatings, such as alkyds and oil-based paints, rely on conventional driers or catalysts to increase reaction rates and achieve faster drying times. However, cure technology can do more than speed up dry times. Typically, formulators measure how tough and durable an alkyd coating is by measuring hardness values through various test methods such as König and pencil hardness. However, hardness values are not the only way to measure how âtoughâ a coating is. By selecting the proper catalyst, formulators can further improve critical performance properties within their alkyd coatings, such as durability, weatherability, non-yellowing over time, and gloss retention. This presentation will highlight how Borchersâ novel catalyst technology can take alkyd coating performance to the next level and add extra robustness.
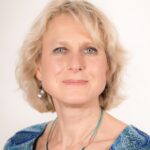
New Ultra-low Viscous, Highly Associative Cellulose Ethers for Acrylic-based Architectural Paints
Helena Wassenius, Nouryon Functional Chemicals
The desired rheology of waterborne, architectural paints can be obtained by combining thickeners of different types and origin that act via different mechanisms. Synthetic associative thickeners form flexible networks via hydrophobic interactions between the polymer chains and the paint components, enabling perfect flow and leveling. Hydrophobically modified cellulose ethers normally have a lower degree of association and a higher molecular weight, giving stronger networks that improve sag resistance but impair the flow and leveling properties of the formulation. In this study, a new ultra-low molecular weight, highly associative cellulose ether is used as a sole thickener in architectural all acrylic formulations. The new thickener gives leveling properties in paint similar to synthetic thickeners (e.g. HEURs) while retaining high sag resistance. This behavior is explained by rheological studies on the viscoelastic properties of a paint series using different thickener systems. The influence of formulation factors such as latex type, dispersant, and wetting agents on the rheological performance of the new thickener is discussed. Results from low-VOC paints of different PVC using the new thickener are presented, including results from an airless spray study. Using a highly associative cellulose ether instead of a thickener system based on synthetic thickeners may also have positive sustainability implications, such as a considerably lowered carbon footprint.
|
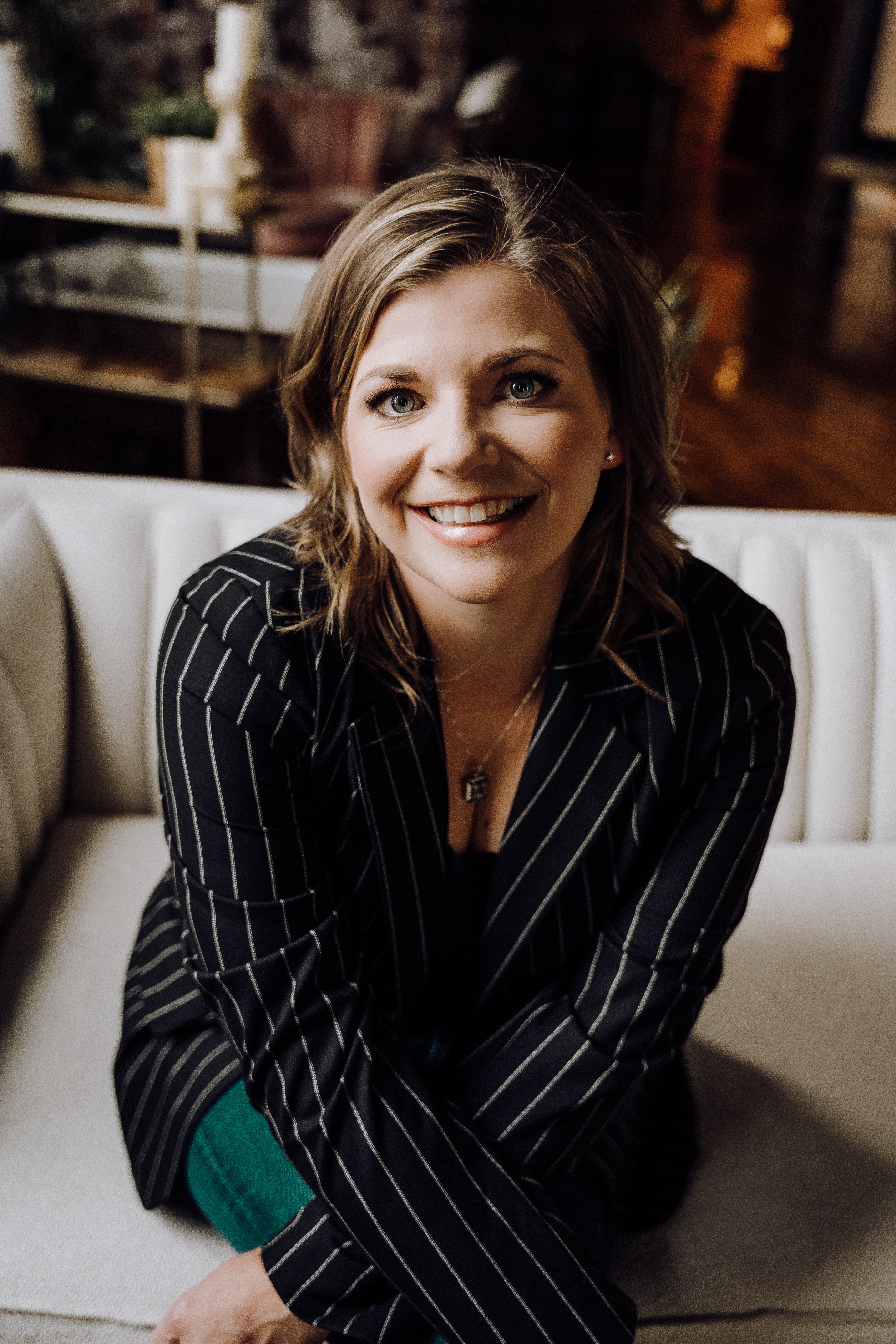
Joshua Ackerman is currently Global Marketing Manager for the CASE, Rubber & Plastic Additives and Sustainable & Natural Products at Univar Solutions, based in The Woodlands, Texas. Operations expertise and previous roles include olefins and isocyanate production at BASF, technical service & development in polyurethane foams at Huntsman, and sales & marketing for sulfide derivatives at Arkema, among other roles in the plastic blending markets and petrochemical decontamination space. Since joining Univar Solutions in 2018, Josh has led responsibilities for product management of surfactant chemistries and is now leading marketing strategy for a range of ingredients & specialty chemical businesses. As a multidisciplinary leader, Josh is passionate about fostering efficiency, business ethics, and sustainability. He received his bachelorâs degree in Chemical Engineering from Michigan Technological University and also holds an MBA from the University of Phoenix.
Mike Stucky is customer sustainability business partner for PPGâs industrial coatings business. He is responsible for creating differentiated value, working closely alongside suppliers and customers to meet their sustainability needs and driving growth through sustainably advantaged products and services. Mike joined PPG in 2003 and held numerous roles in PPGâs Automotive OEM Coatings business, including those in product, engineering, chemical management, and acquisition integration. He earned a degree in chemical engineering as well as an MBA from Michigan State University.
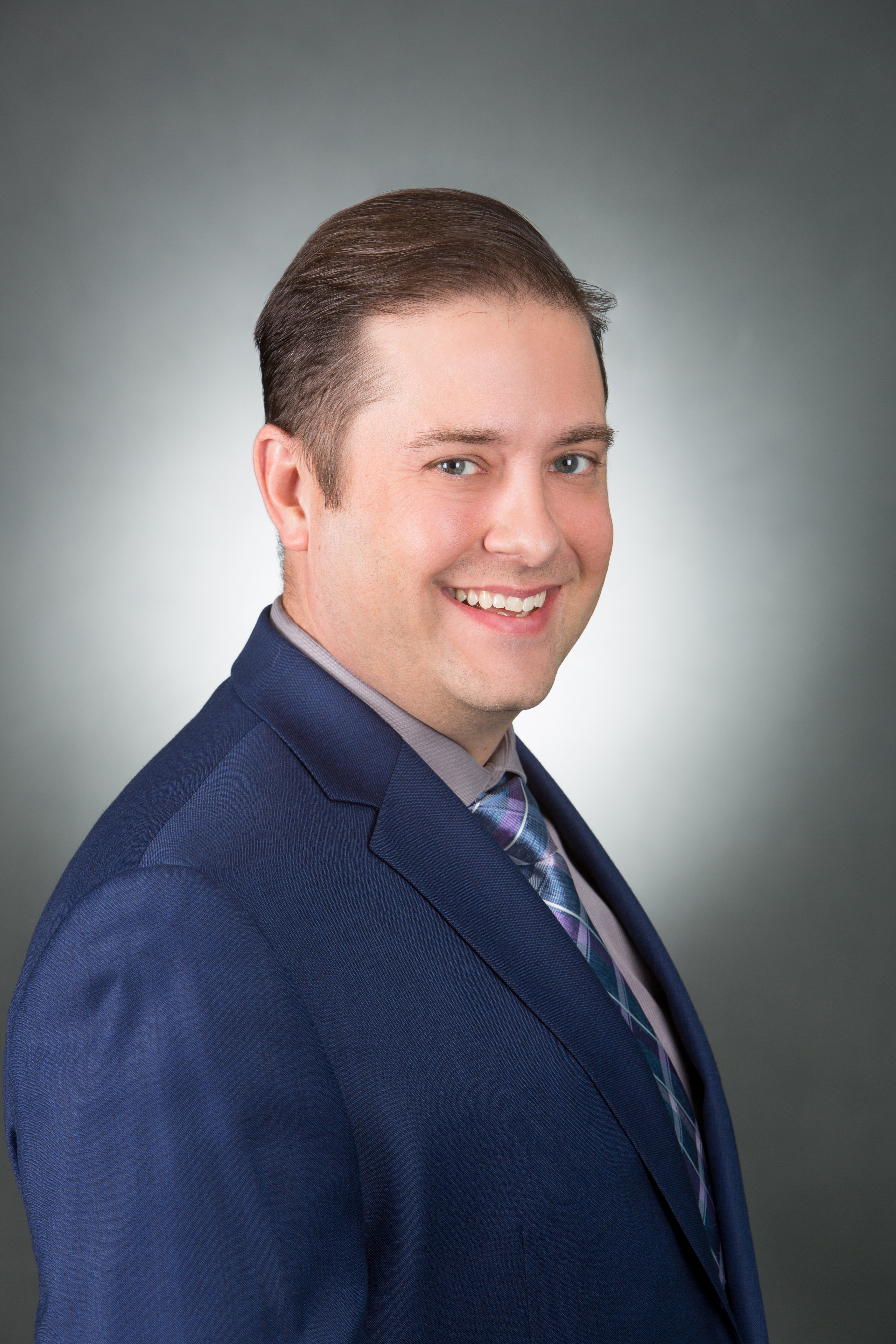
Scott Simmons is the Global Director of Environmental Social and Governance at Barentz. Scott joined Barentz in 2018 and is responsible for developing and implementing Barentzâ global sustainability strategy. Prior to joining Barentz Scott was on the North American regulatory team at Lubrizol.
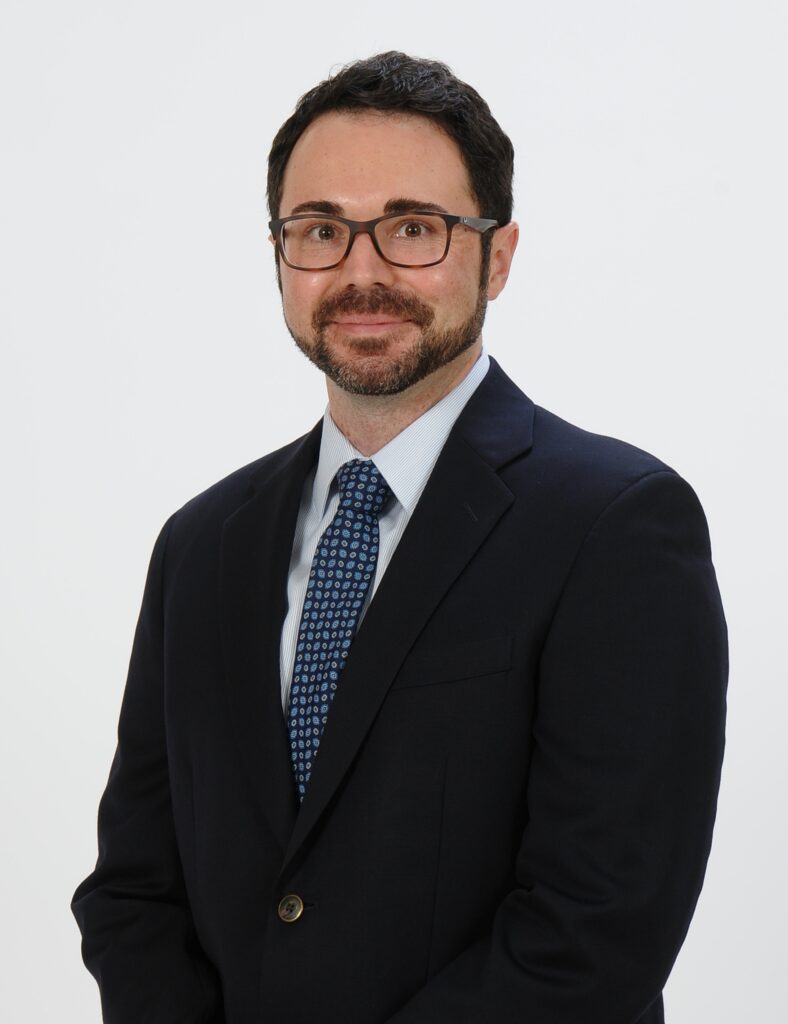
Chuck Hardy is Michelmanâs Global Director of Sustainability and R&D Systems. Chuckâs responsibilities include design and implementation of Michelmanâs global sustainability strategy, and management of the physical and virtual capabilities Michelman uses to design and commercialize new products. Chuck earned a Bachelor of Science degree in Chemical Engineering at the University of Florida.
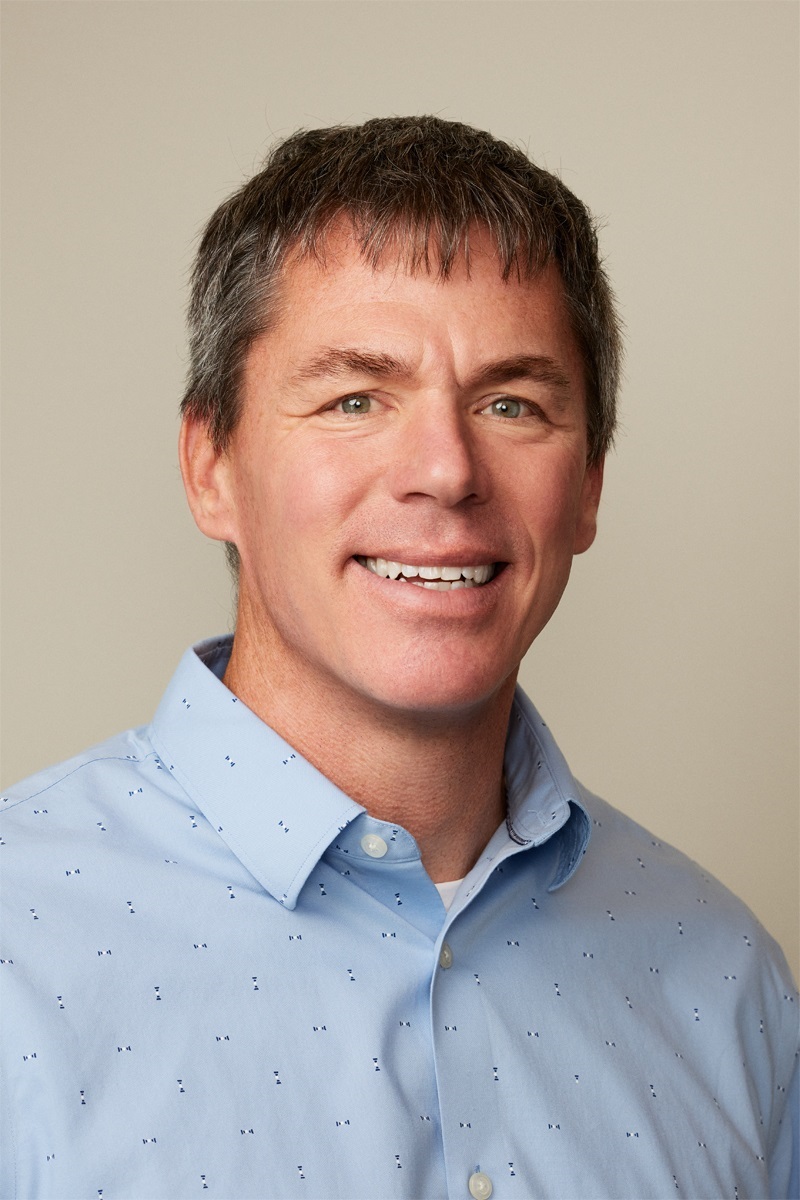
Raymond Somich is the Global Marketing Group Director for Synthomerâs Coatings and Construction Division.   Raymond is a member of Synthomerâs enterprise Sustainability Communications Council and Synthomerâs North America Diversity Equity and Inclusion committee.Raymond has more than 22 years of experience in the chemicals industry with a specialization in infrastructure, road highway safety, and construction including architectural and industrial coatings. His chemistry application experience includes acrylics, epoxies, styrene-butadiene, polyurethanes, silicone and formulated materials. He work experience includes businesses at DuPont, Celanese and Olin Corporation while with Dow Chemical Company.Raymond holds a Bachelor of Science degree specializing in Marketing and completed his Masters in Business Administration at Bowling Green University. He also holds a Six-Sigma Green Belt.
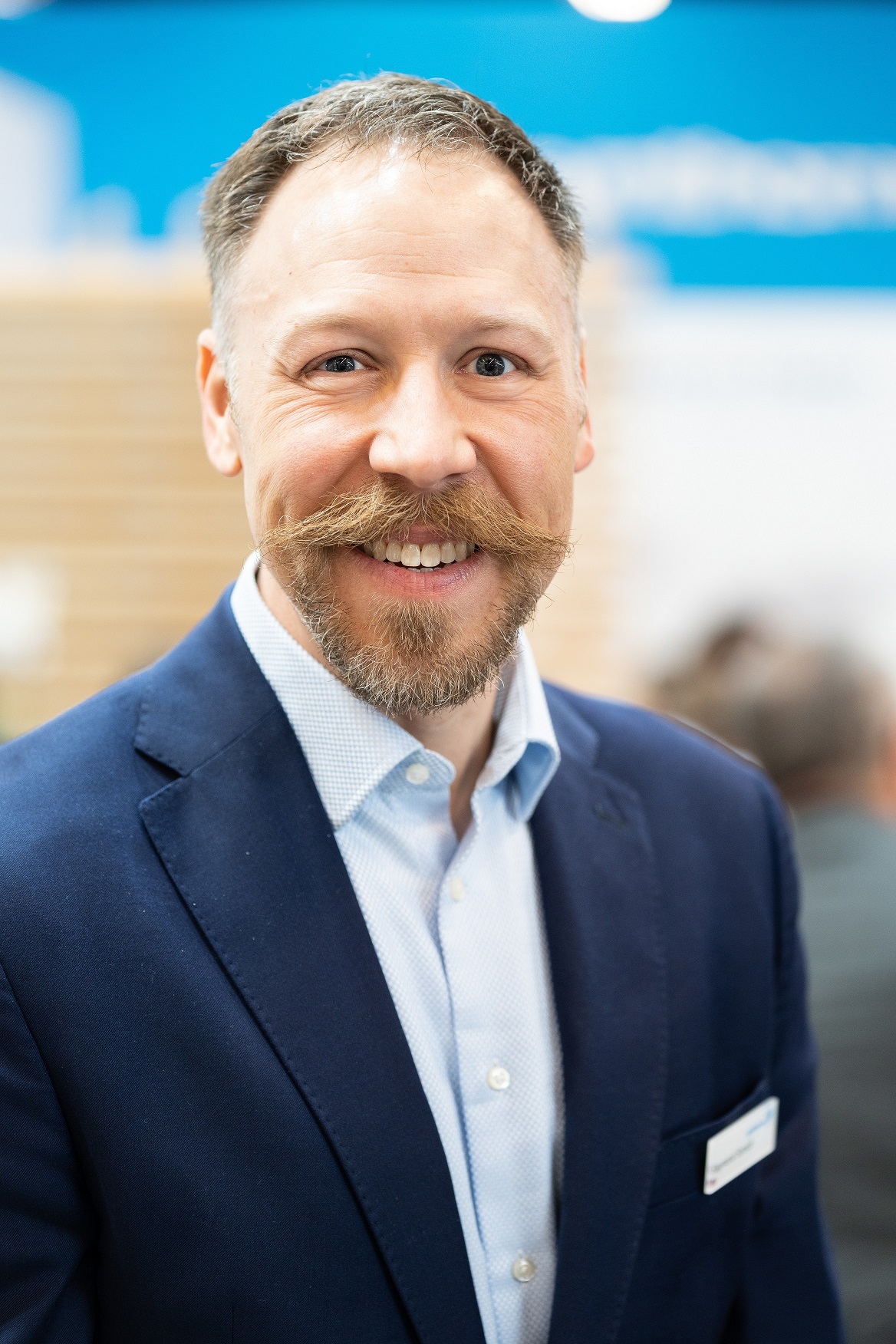