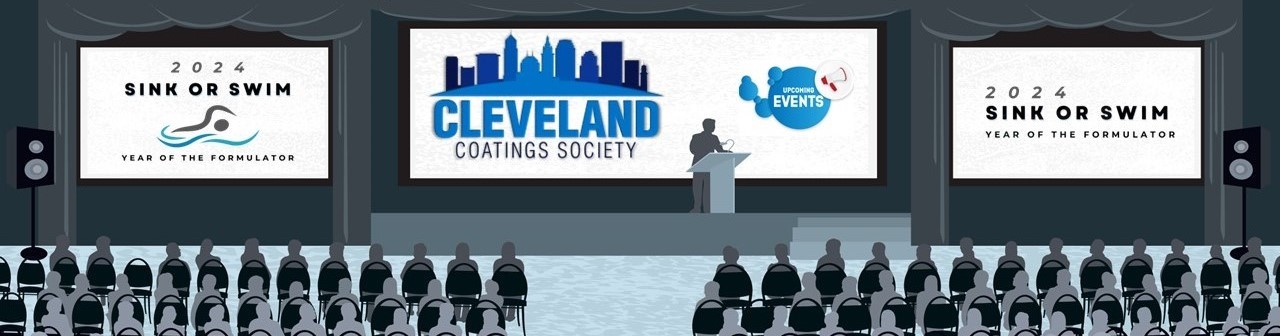
2024 SOS Speakers

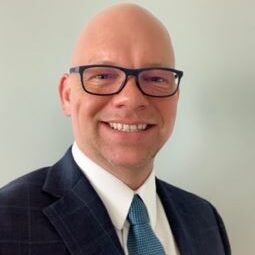
Andrew Recker
Keynote Speaker
Intentional Innovating Through Fail Fast Formulating
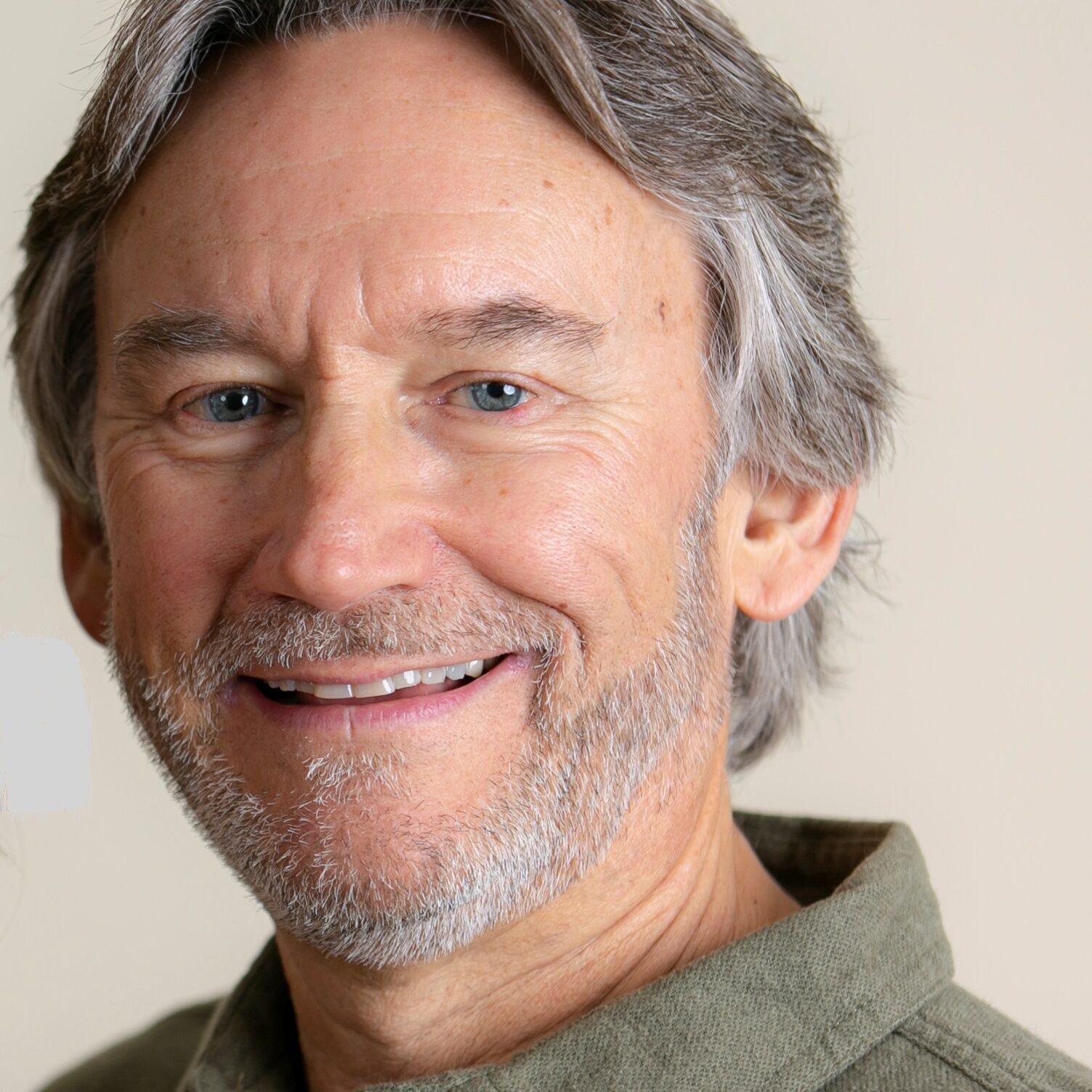
Chuck Shearer
Northeast Field Technical Service Representative, Covestro Coating Resins
New 1K-Waterbased Resin for Residential Vinyl Window Coatings
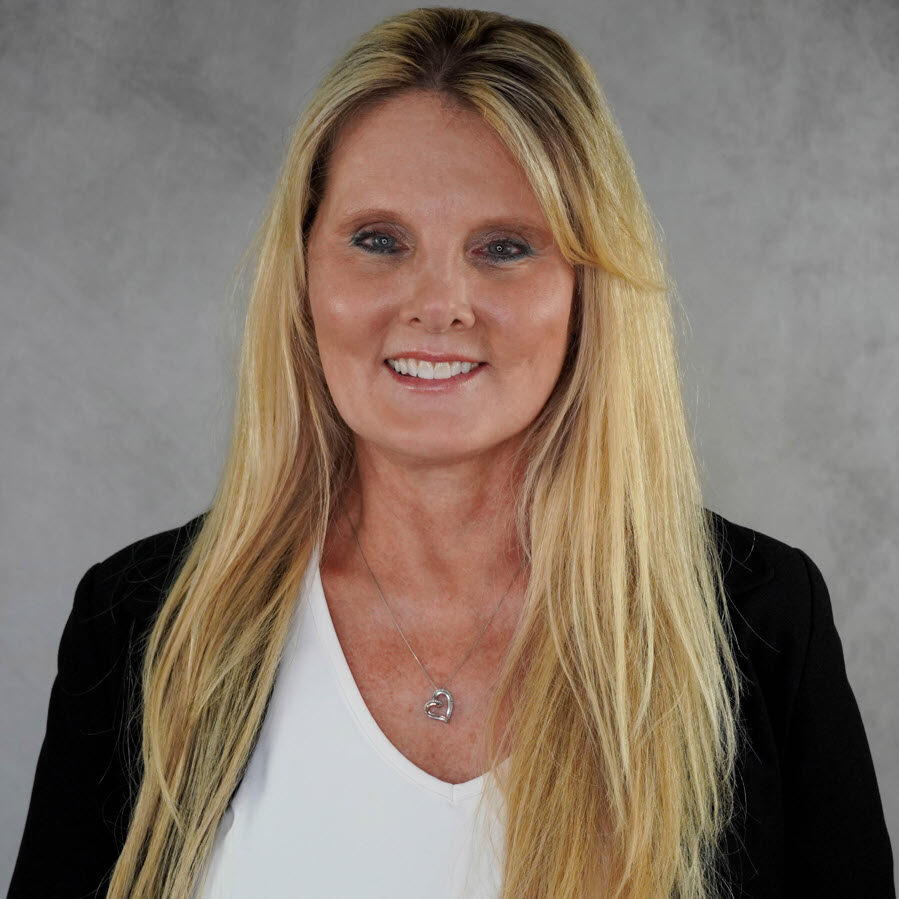
Debora Hense
Technical Director, Stonebridge Coatings Laboratory, Inc.
Formulators’ Bio-Toolkit: A Deeper Dive Into Soy-Based Raw Materials for Waterbased Coatings
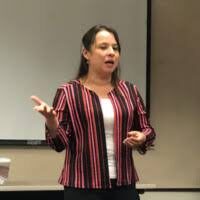
Milena Garay-Tovar
Applications Scientist, The Lubrizol Corporation
Bio-based High Solids Polyamide Polyols for Protective Coatings
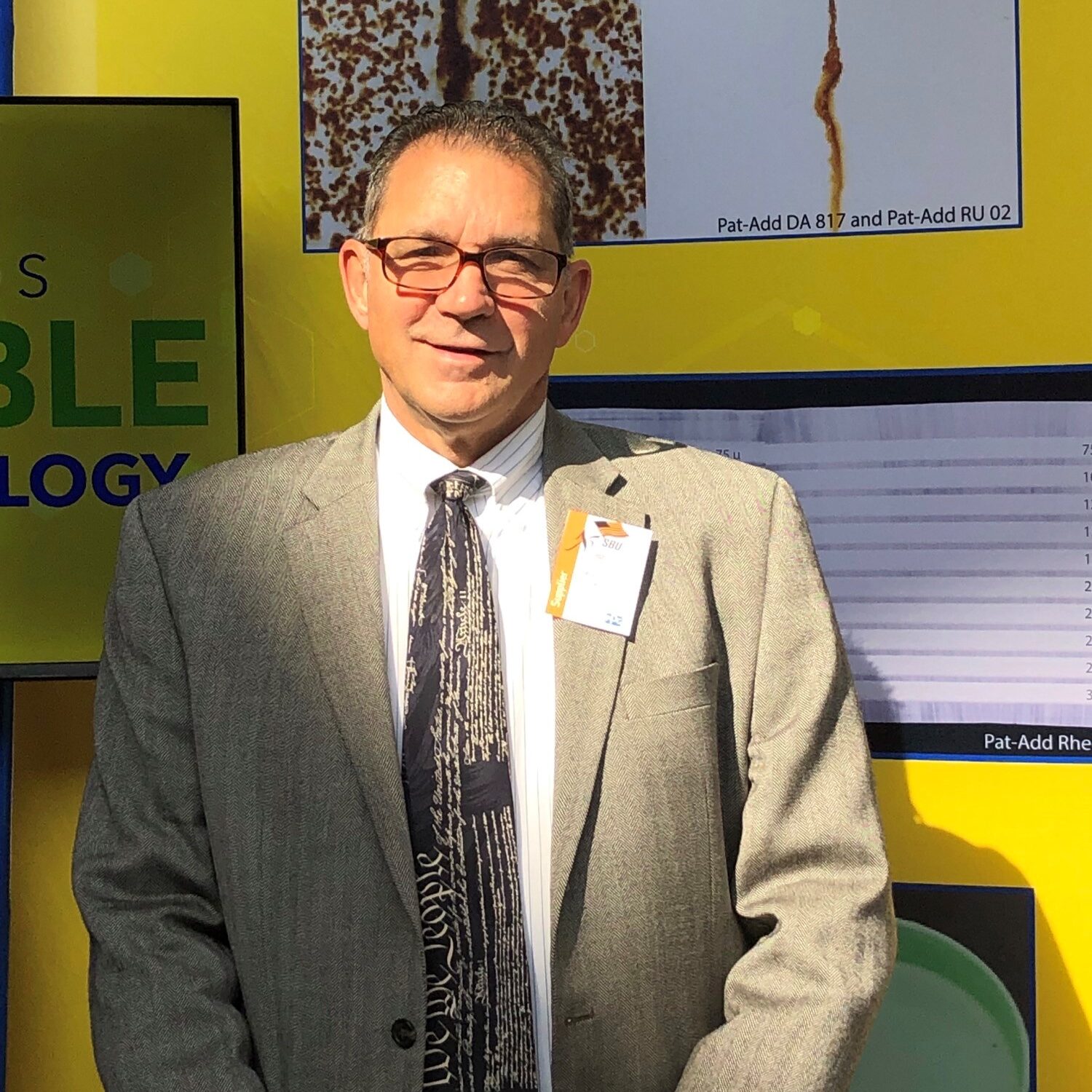
Glenn Baroone
Sales, USA Patchem
What Does Sustainability Mean To You?
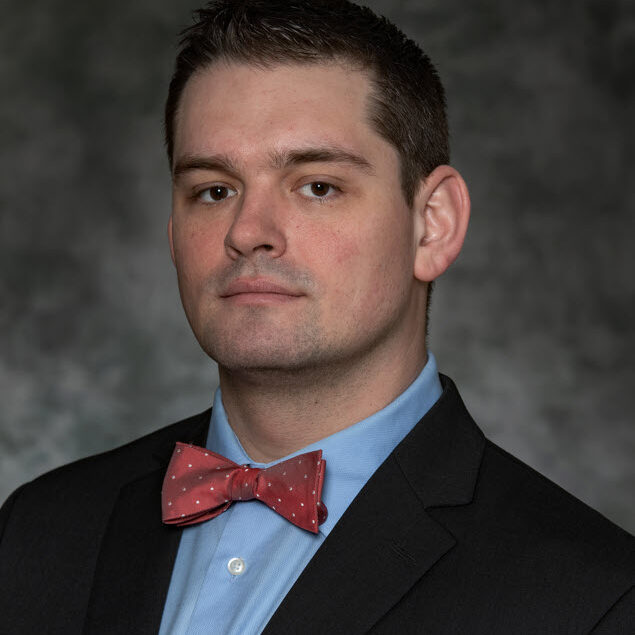
Israel Skoff
Technical Marketing Manager, Lubrizol Advanced Materials, Inc.
High Solids TEA-free Waterborne Polyurethane Dispersions
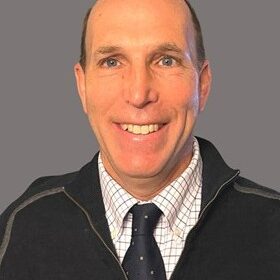
Jeffrey Hamilton
Technical Service Engineer, Arkema, Kynar Coatings Group
Advances in 1K PVDF/Acrylic Hybrid Dispersion and their Applications
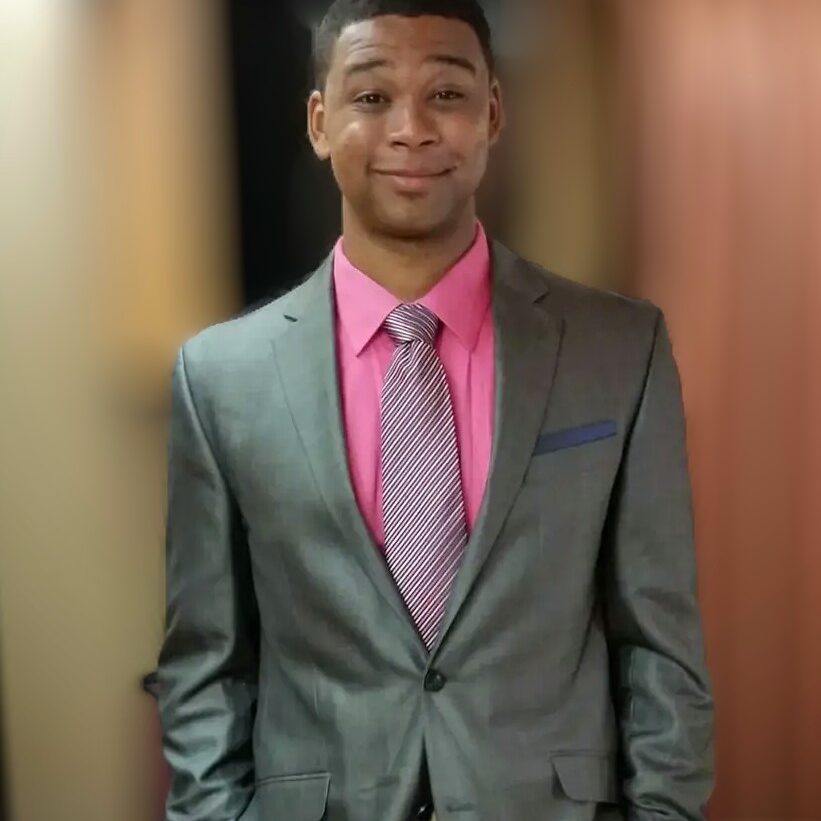
Ramon Lozada
Global Product Manager, Vibrantz Technologies, Architectural Coatings
Sustainable technology enhances the future of colorant tinting systems
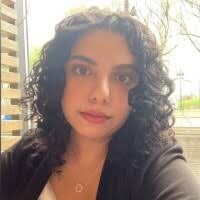
Sadia Younas
Market Development Manager, Vencorex
Novel Polyisocyanates for Flexibilizing Polyurea Coatings
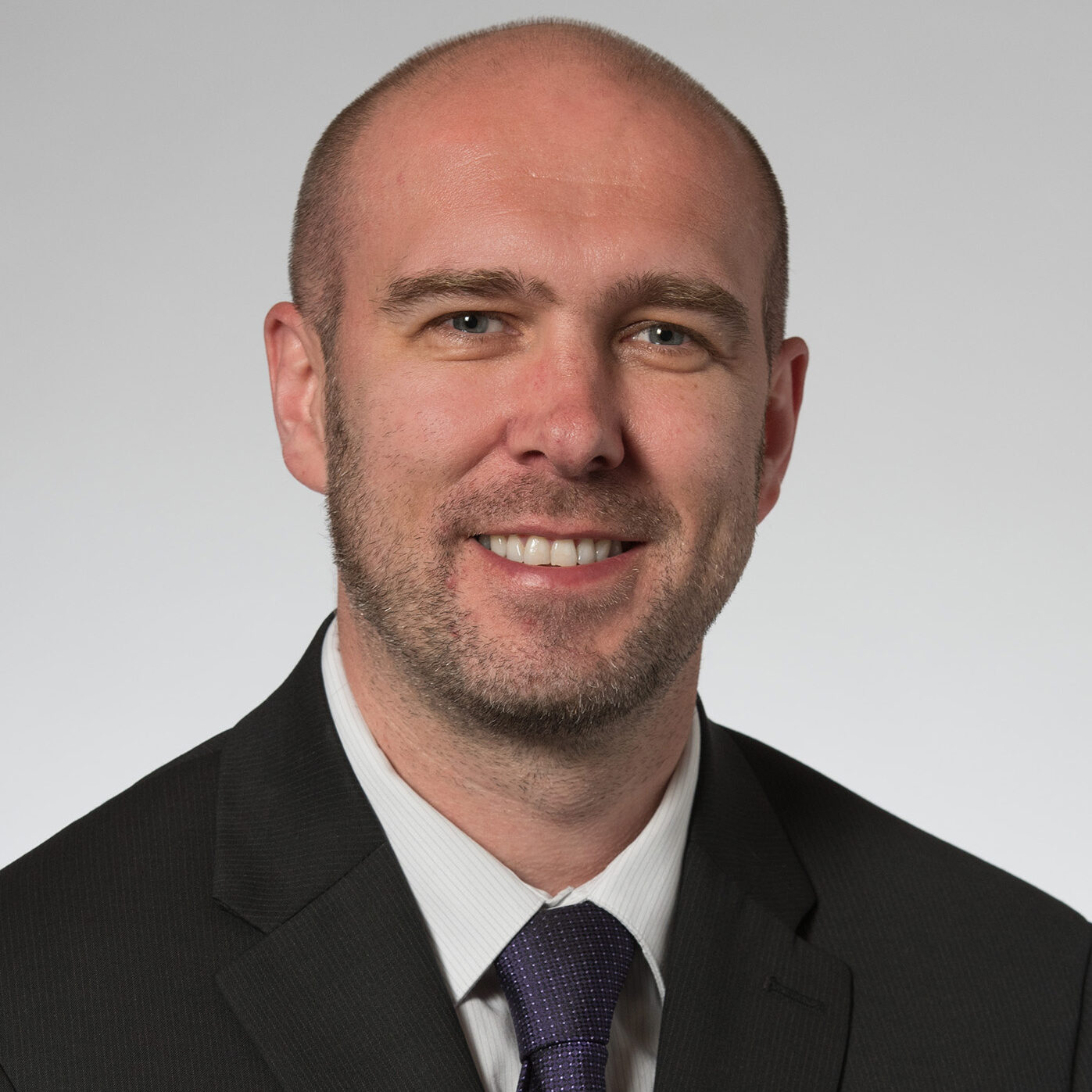
Matthew Dunn
Business Development Manager, Lubrizol Advanced Materials, North America
100% Active Dispersants for Aqueous and Non-Aqueous Coatings
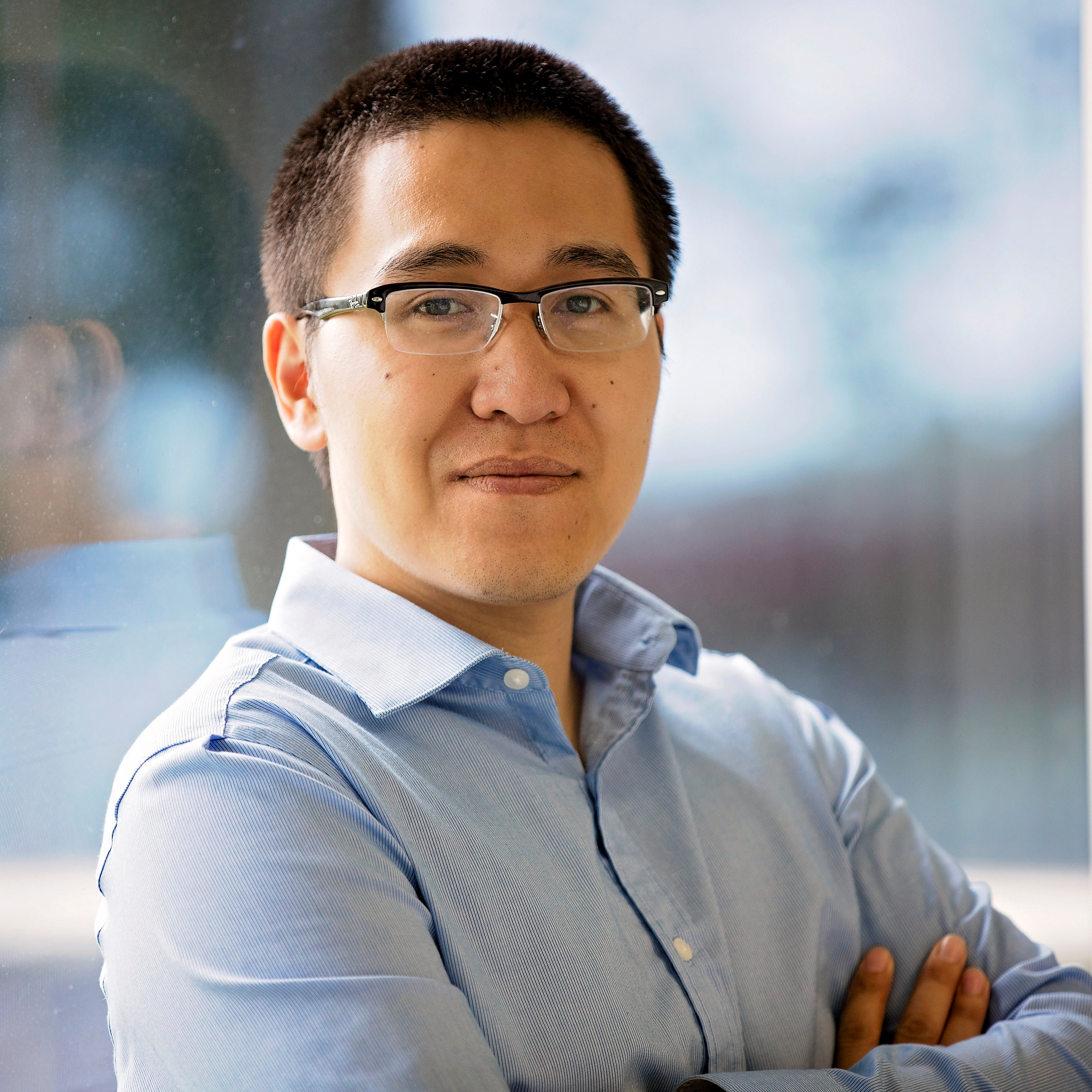
Dr. Ziniu Yu
Technical Service Manager - Coatings at W. R. Grace
Easy to Process: New Silica Matting Agent for Energy Curable Coatings
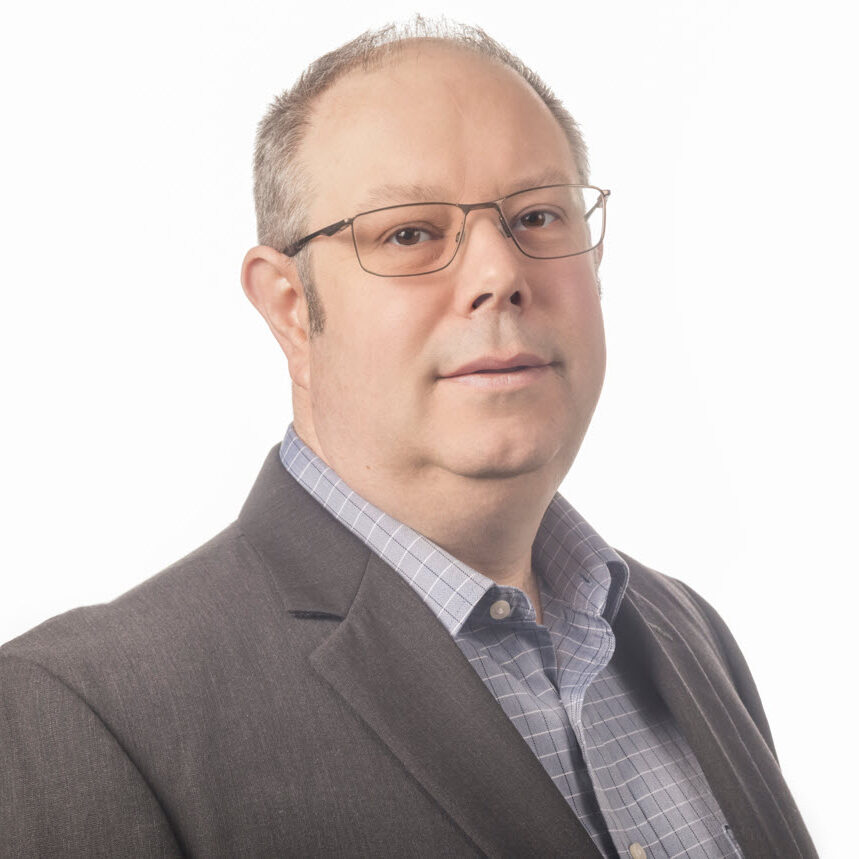
Mike Jefferies
Mike Jeffries, Field Technical Service Manager, Covestro
Looking Beyond Performance Specifications to Capitalize on New Opportunities in Factory Applied Coatings
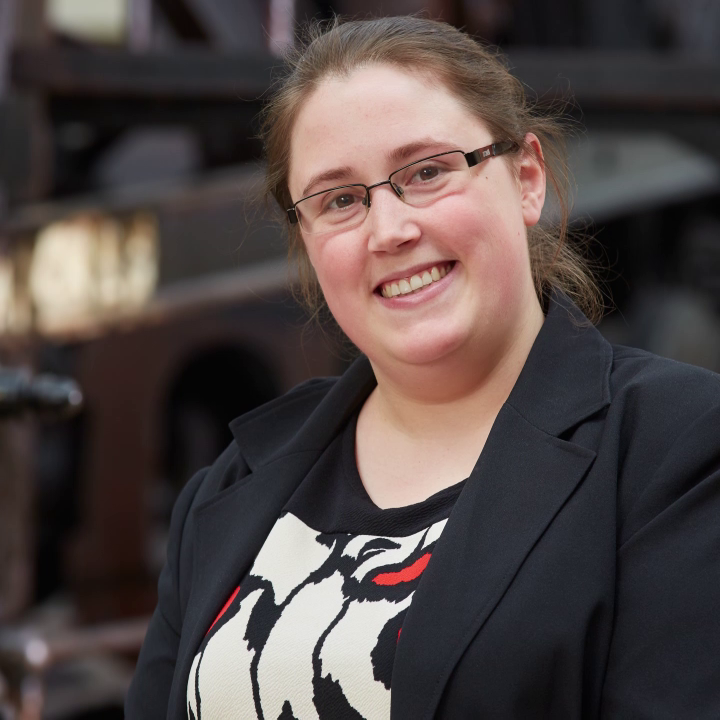
Stephanie Vanslambrouck
Chief Scientist – Technical Manager, EMCO-Inortech
Elongation in Epoxy membranes: a comparative study of formulation modifications and plasticizer effects
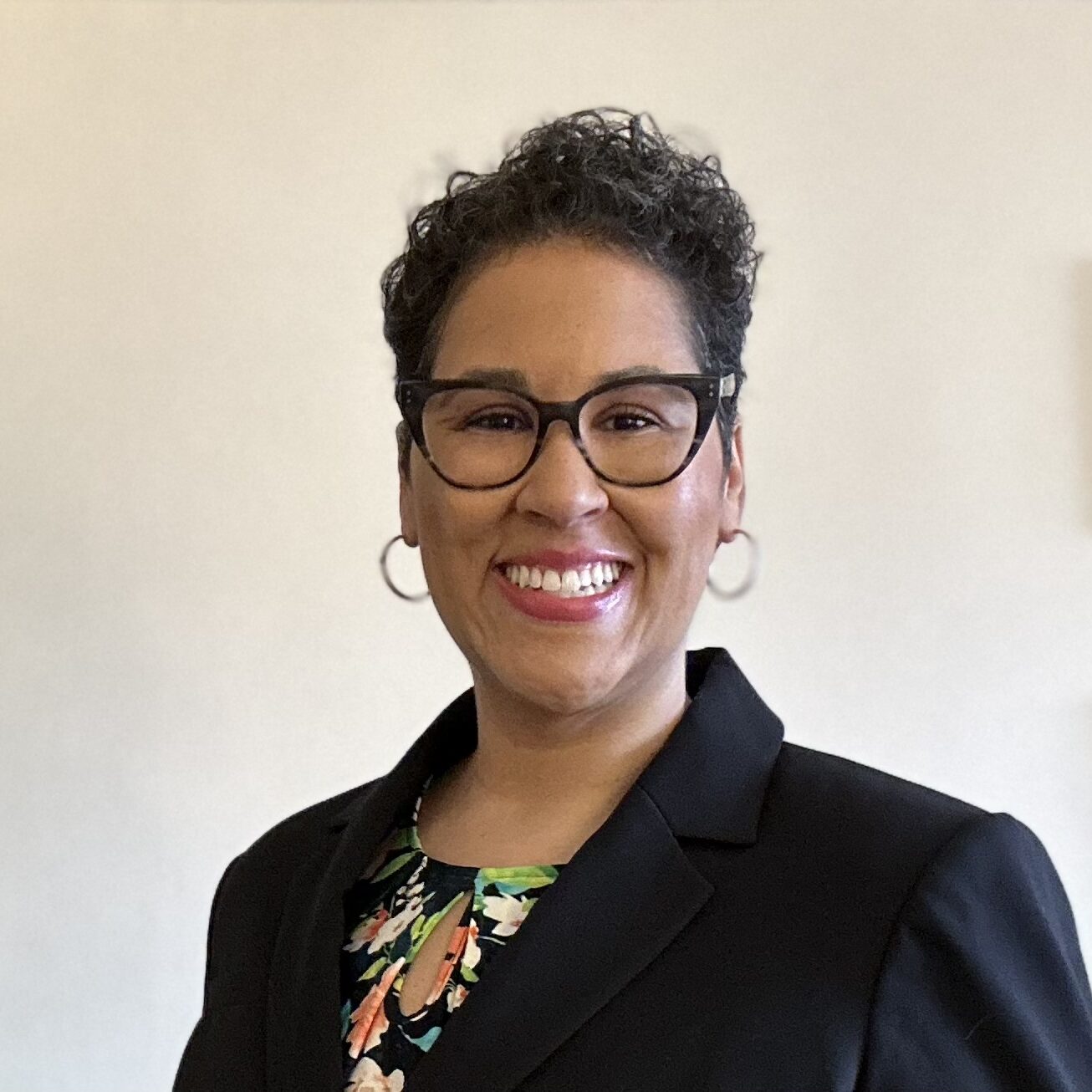
Stephanie Yates
Advanced Application Development Engineer, Momentive Performance Materials
Silicone-Based PFAS-Free Solutions for Architectural Coatings
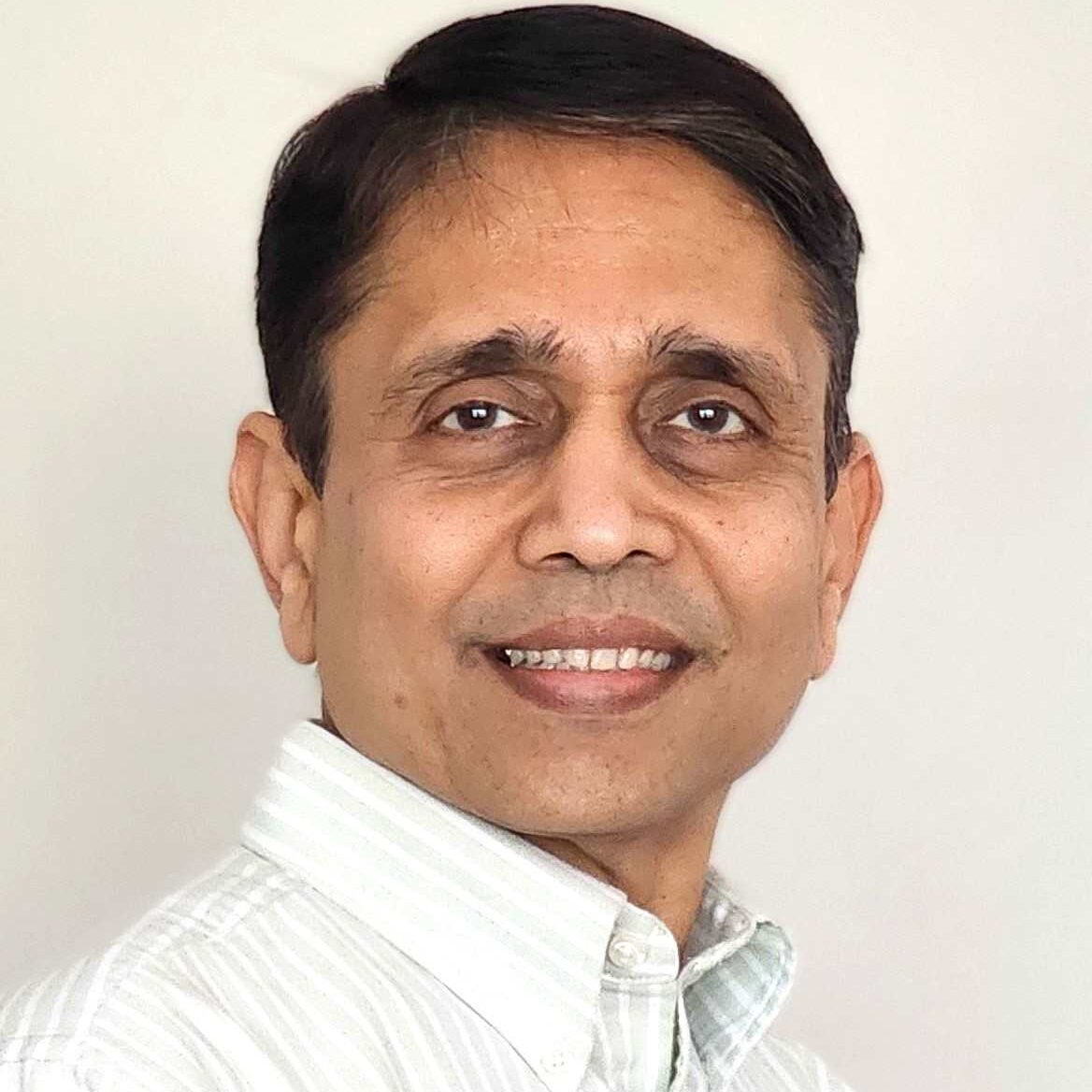
Dr. Gautam Haldankar
Technical Manager at Allnex
Novel Resins and Formulation Approaches for Challenging Regulations
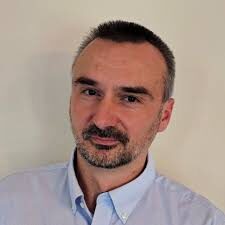
Gabor Erdodi, Ph.D.
Senior Scientist, The Lubrizol Corporation
Bio-based High Solids Polyamide Polyols for Protective Coatings
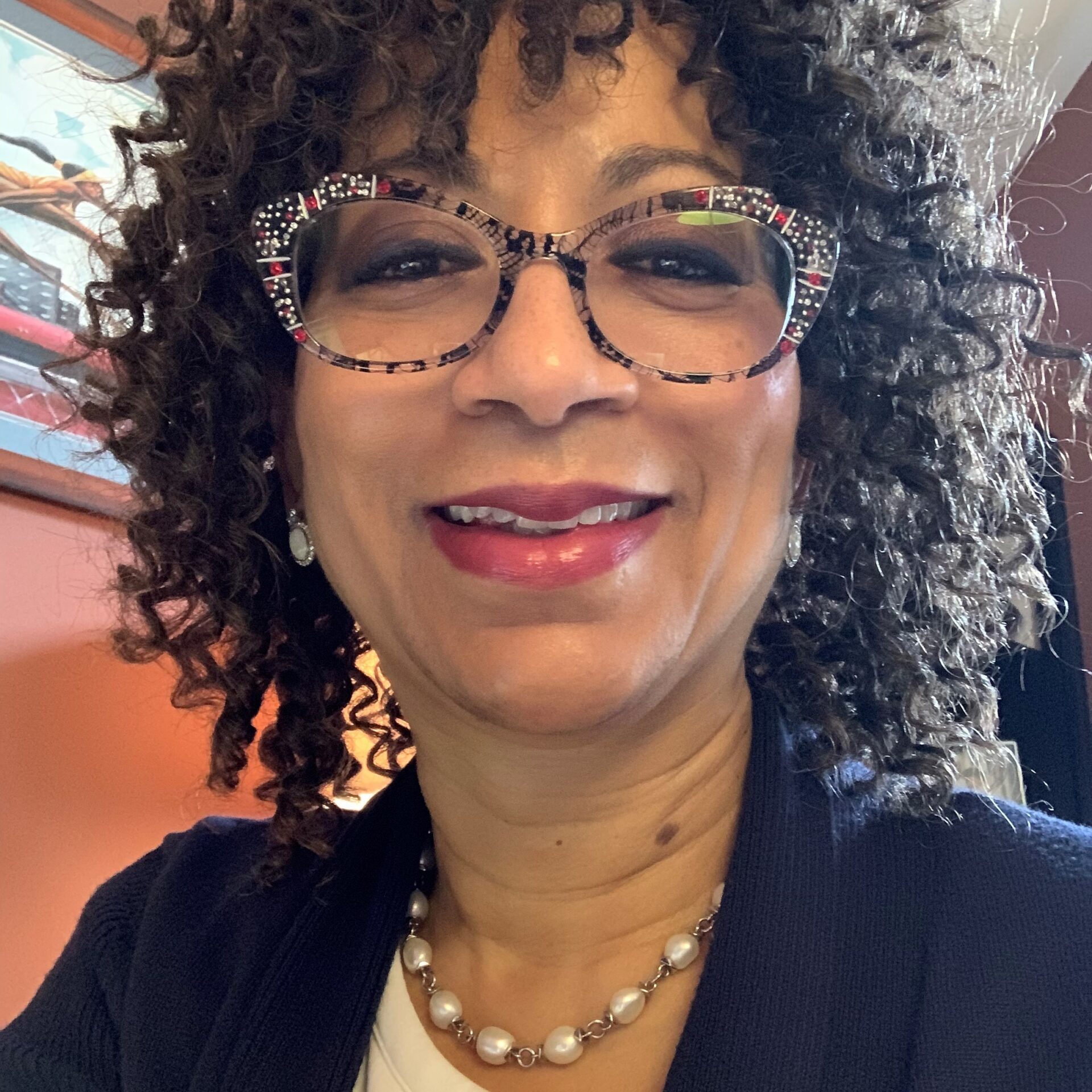
Latoska N. Price, M.S.
Regional Technical Manager Coatings, Americas, Synthomer
New Biobased Versatile Binder for Architectural Coatings
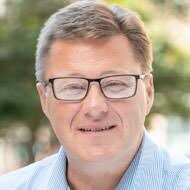
Bruce Berglund
Sales, Business Development and Technical Support Manager at CHT USA
High Performance Wood Coating Additives
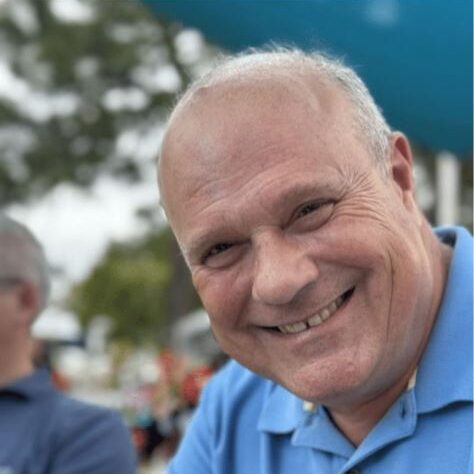
Mathias Dubecq
Business Development Manager for ADI and Waterborne Technologies at Wanhua Chemical (America)
Polyaspartic Coatings
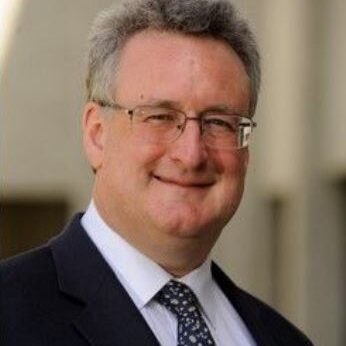
Jim Reader
AT Industrial & Transportation - CAD Applied Technology - Coating Additives
Predicting Defoamer Performance in Different Waterborne Coating Formulations
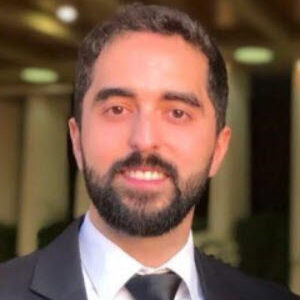
Bruno Soares Dário
TS&D Scientist for CASE at Indorama Ventures
Incorporation of Nonionic Reactive Surfactants and Resin Stability
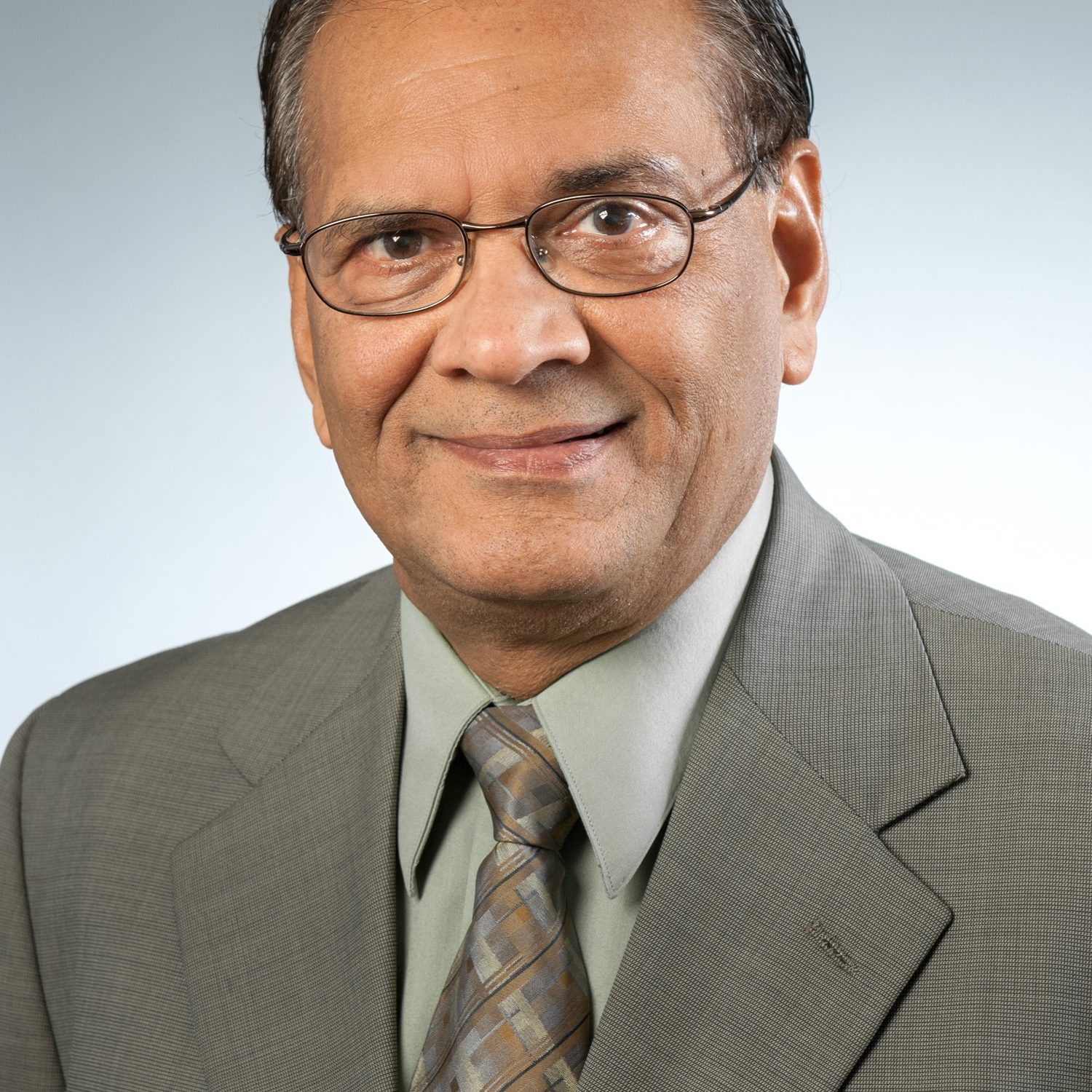
Dr. Nemi Jain
Senior Technical Manager, Center of Excellence in Analytical Sciences
Global Supply Chain, Sherwin-Williams Co., Cleveland
Analytical Sciences for Non-Analytical Professionals
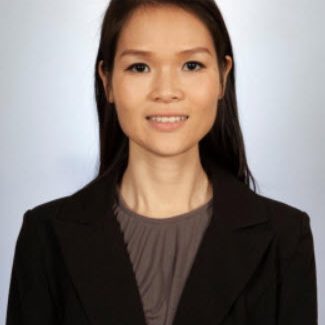
Vy Vo
Technical Marketing Manager for Orion Engineered Carbons’s Coatings segment in North America
Reducing Carbon Footprint with Sustainable Carbon Black